Hey community,
On July 12th, we proudly announced that the first batch of the Seeed Studio BeagleBone Green were successfully manufactured at the Telstar Factory in Bac Giang, Vietnam. A month ago, we announced our partnership with Telstar, championing our shared vision of decentralized, open manufacturing (a good read below). We are excited to see our first batch of products manufactured in Vietnam, driving the future of open, localized manufacturing that benefits all.
Telstar Factory is globally certified and meet international quality standards. They possess advanced technological facilities and equipment, which enable them to produce high-quality and high-precision electronic components and parts. Additionally, Telstar has an experienced workforce with professional knowledge and skills in the field, ensuring the accuracy and efficiency of the production process. Moreover, they adhere to strict quality management standards and commitments, ensuring that the products meet customer needs and expectations in terms of functionality, performance, and reliability.

In this blog, let’s follow our project manager Mandy, to explore how we manufactue Seeed Studio BeagleBone Green in Vietnam. The Seeed Studio BeagleBone Green product manufacturing process involves multiple steps, including PCB preparation and loading, solder paste printing, components placement, reflow soldering, AOI and X-ray inspection, DIP and wave soldering, testing and quality check, as well as the final packing.
1. PCB Preparation and Loading
The first step in SMT manufacturing is to prepare the PCB. A PCB loader is used at the start of the production line for loading PCB to the line, which is to provide a fixed position for the next phase of the process.
2. Solder Paste Printing
This stage is crucial during the SMT process where a printer applies solder paste using the stencil. Solder paste acts as a temporary adhesive to keep the surface mount components in place. The stencil ensures that the paste is applied accurately and consistently across the PCB. It is essential that the right amount of paste is applied to each pad, otherwise, there will be no connection established when the solder is melted in the reflow oven.
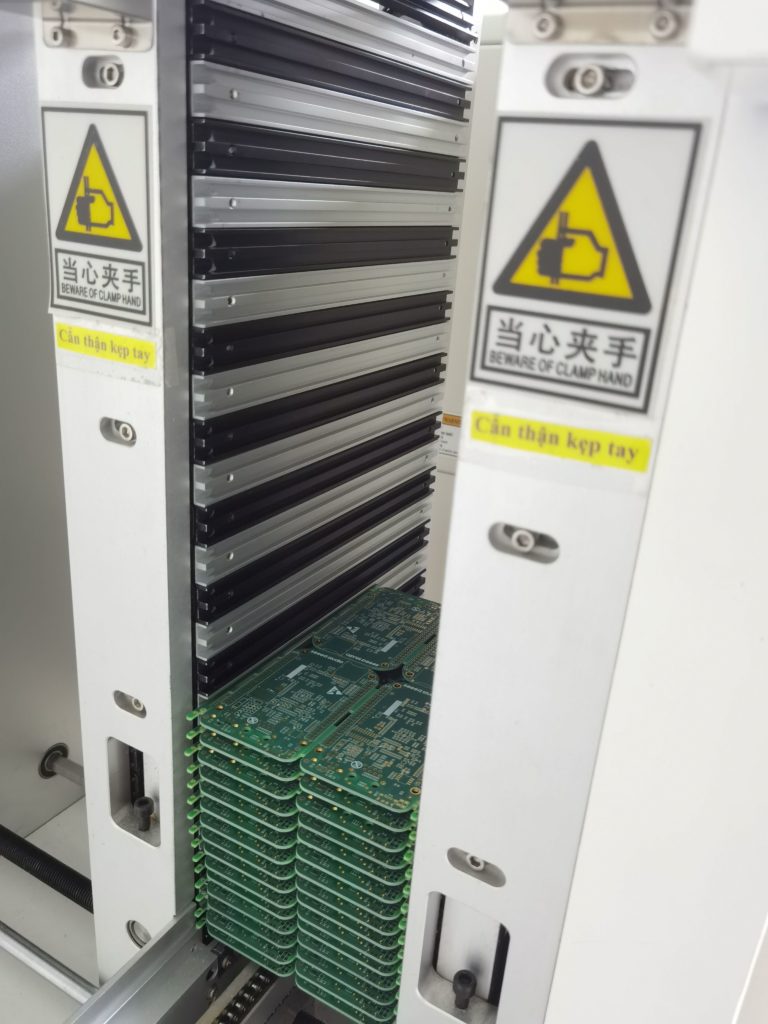
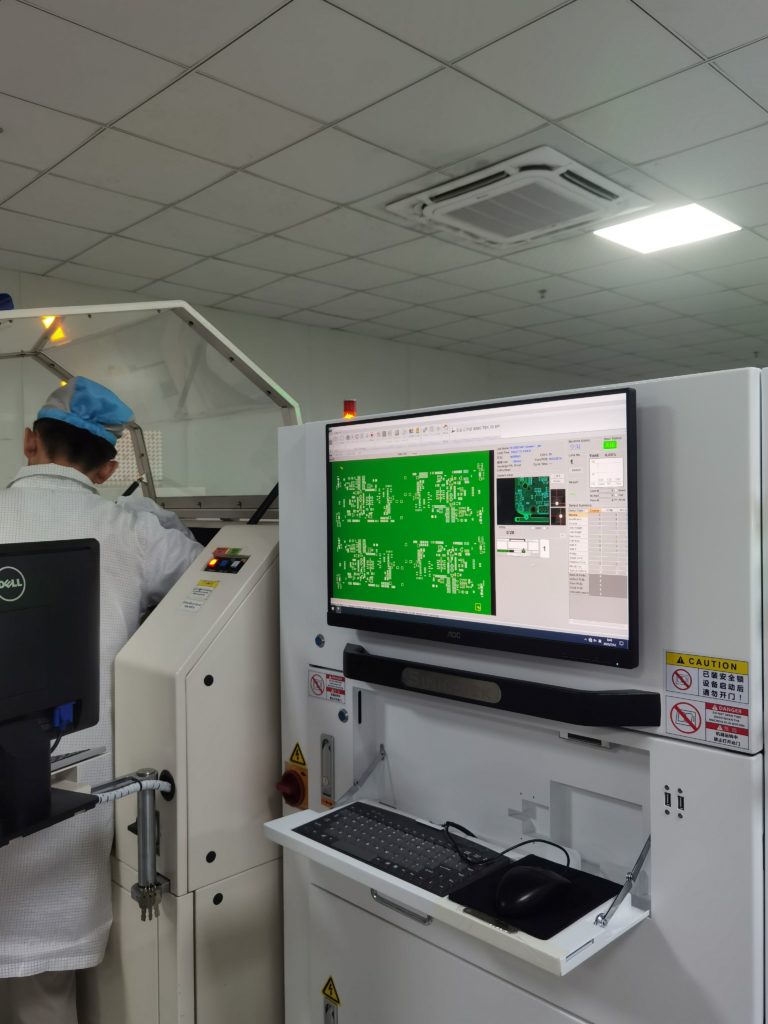
3. Components Placement
After verifying that the printed PCB has the appropriate quantity of solder paste, it proceeds to component placement. The placement machine precisely picks up each component and affix it to its designated location. The PCB is transported by a conveyor belt while the machines accurately and rapidly mount the electronic components on it. Precision is essential in this process since any incorrect placement can be a significant expense and require time-consuming rework.
4. Reflow Soldering
The next step is to reflow the PCB. Reflow is the process of heating the solder paste to melt it and create a permanent bond between the components and the pads. The PCB is placed in an oven, and the temperature is carefully controlled to ensure that the solder paste melts and re-solidifies correctly. This process creates a reliable and robust connection between the components and the PCB. Although it may seem like a simple part of the process, the correct reflow profile is crucial to guarantee satisfactory solder joints and prevent damage to the components.
5. Automated Optical Inspection (AOI)
After soldering, the board is subjected to cleaning and quality inspection to identify any defects. Automated Optical Inspection, also know as AOI, is a process used in manufacturing to inspect products or components using high-resolution cameras and software programs. It can identify issues such as missing components, incorrect component placement, or soldering defects.
6.X-ray Inspection
X-ray inspection is to penetrate non-metallic substances in objects through X-rays without damaging the object being inspected. This technique is used to detect faults such as the quality of BGA component soldering and whether there are any short circuits present. While AOI uses high-resolution cameras to detect faults in products or components’ external surface, X-ray inspection penetrate products or components’ internal structures, such as detecting short circuits, missing solder, and other defects in products like lithiumion batteries and IC chips.
Both of the inspection processes are critical, especially for high-volume production, as it allows for quick detection and correction of any manufacturing defects.
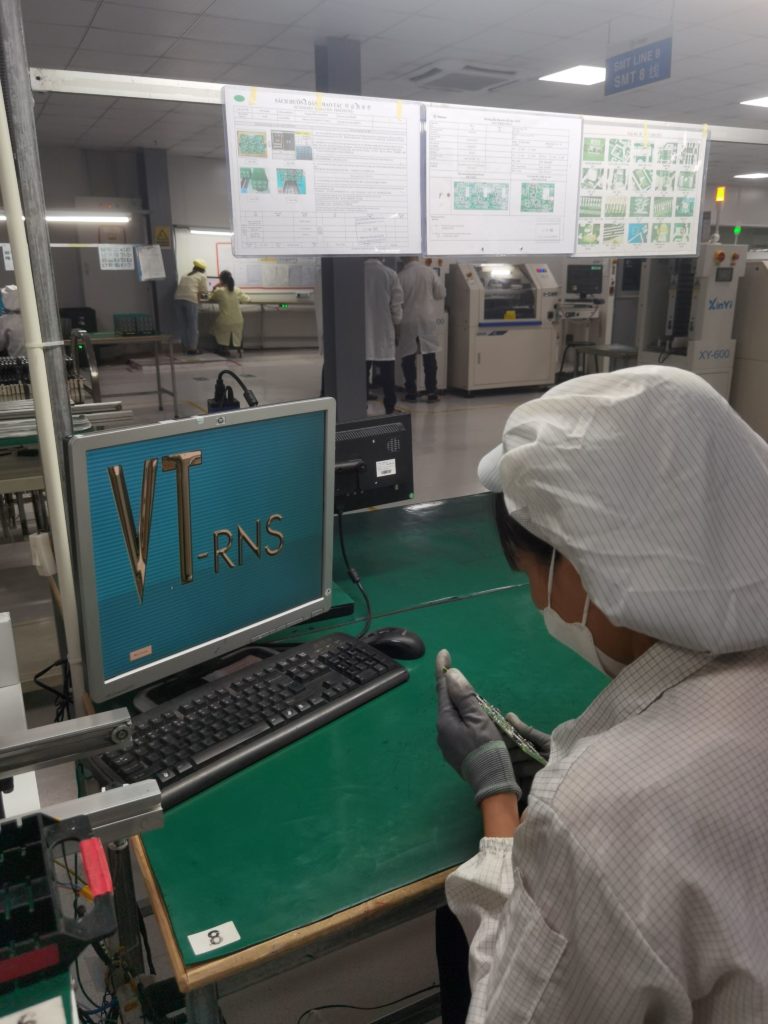

7. DIP & Wave Soldering
Dual In-line Package (DIP) and wave soldering are additional steps in the manufacturing process used for through-hole components. DIP is a type of through-hole technology that uses a DIP socket to put in electronic components such as resistors and diodes. Wave soldering is a process that uses a molten solder wave to solder the through-hole components onto the PCB. These processes ensure that the through-hole components are accurately and securely mounted onto the PCB to produce a reliable and functional electronic device.
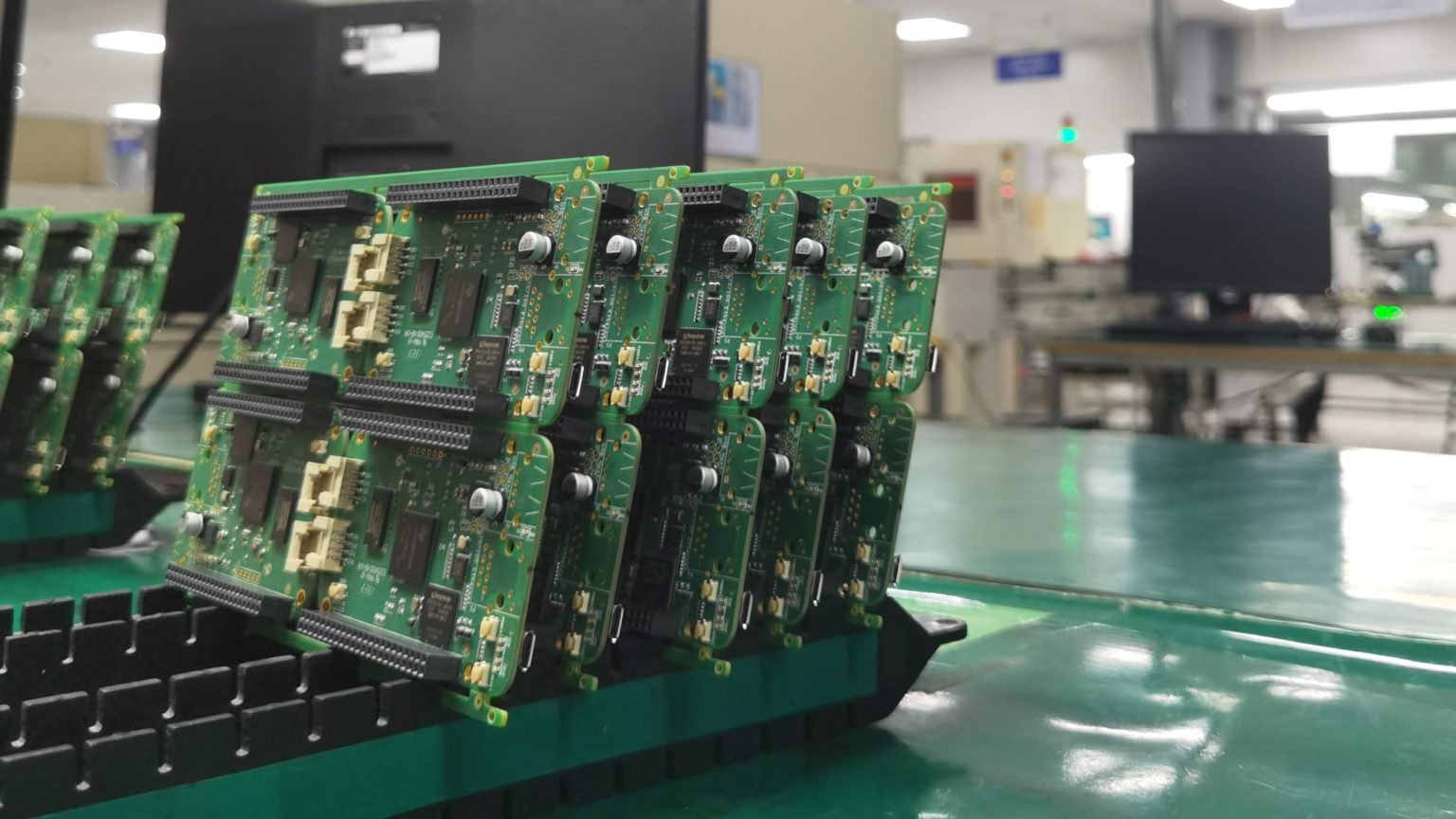
8. Functional Testing & Quality Check
We are almost there! Now you can see the semi-finished BeagleBone Green. The final stage is functional testing. These tests examine the complete assembly instead of individual components, guaranteeing that the products will operate appropriately. They act as the final stage between manufacturing and the market, ensuring the product is of high quality, reliable, and ready for distribution.
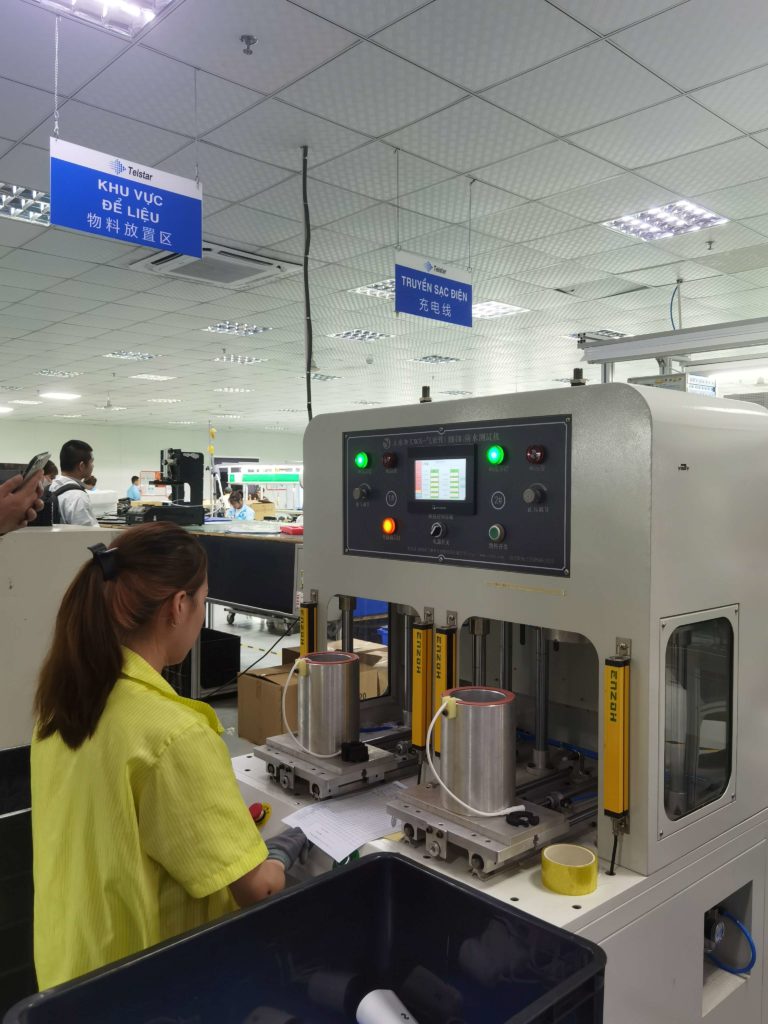
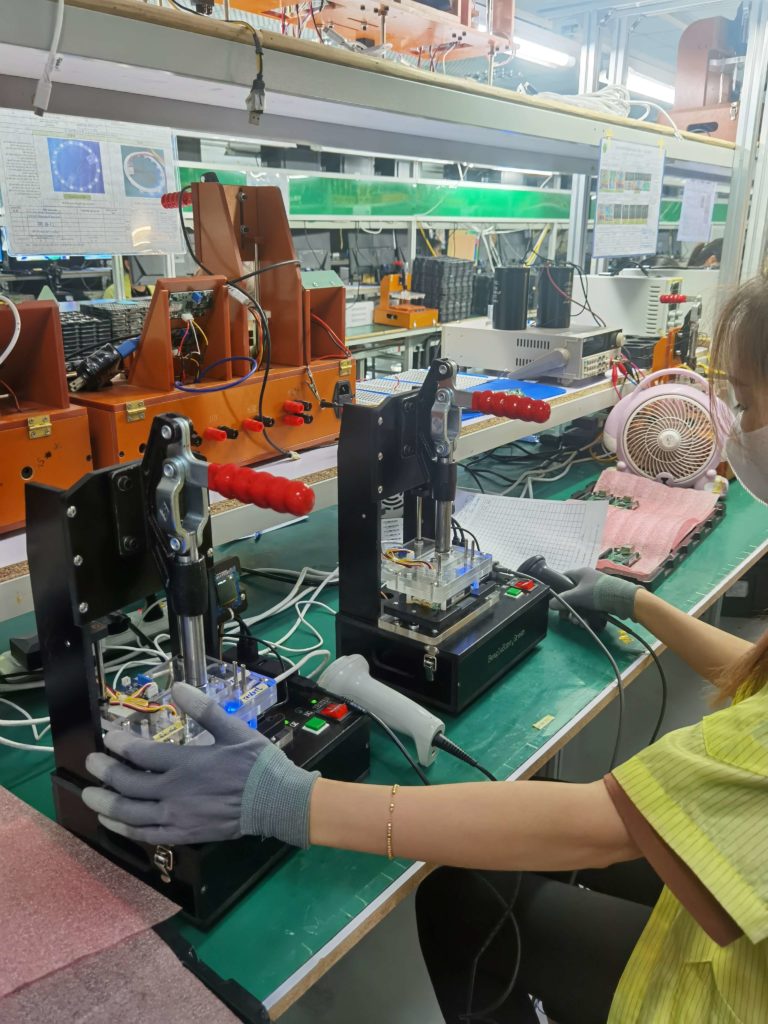
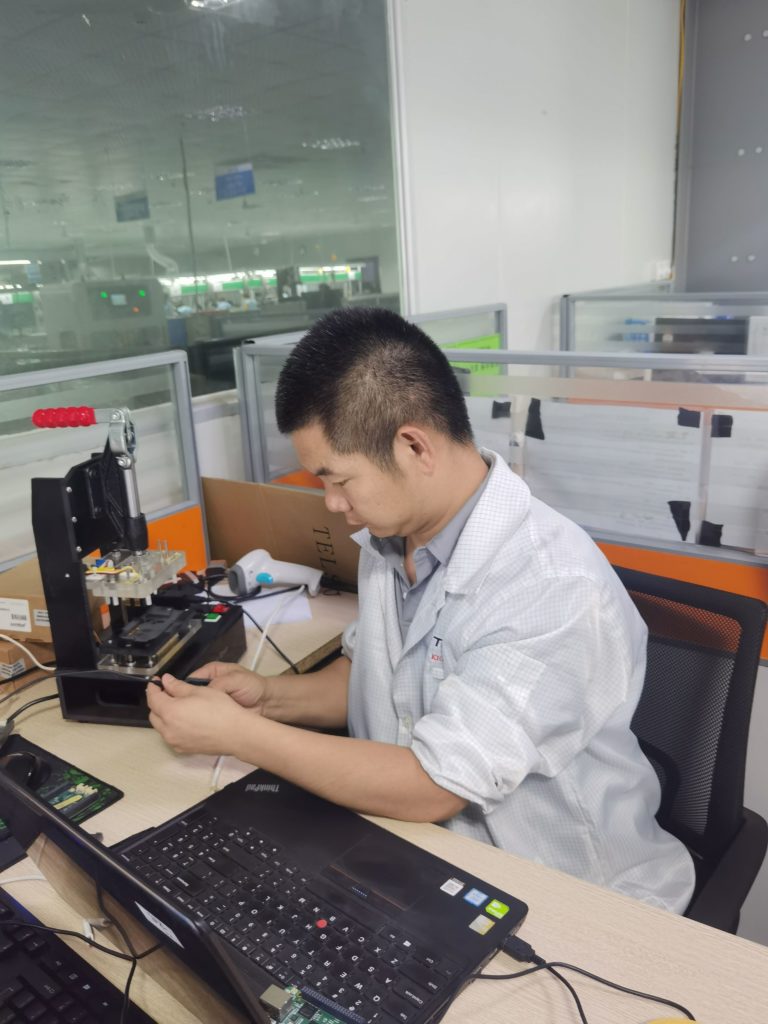
9. Packing
The packing process ensures that the products are suitably packaged and protected, ready for distribution to you. We want to protect the products from damage during transportation and ensuring that they reach you in excellent condition.
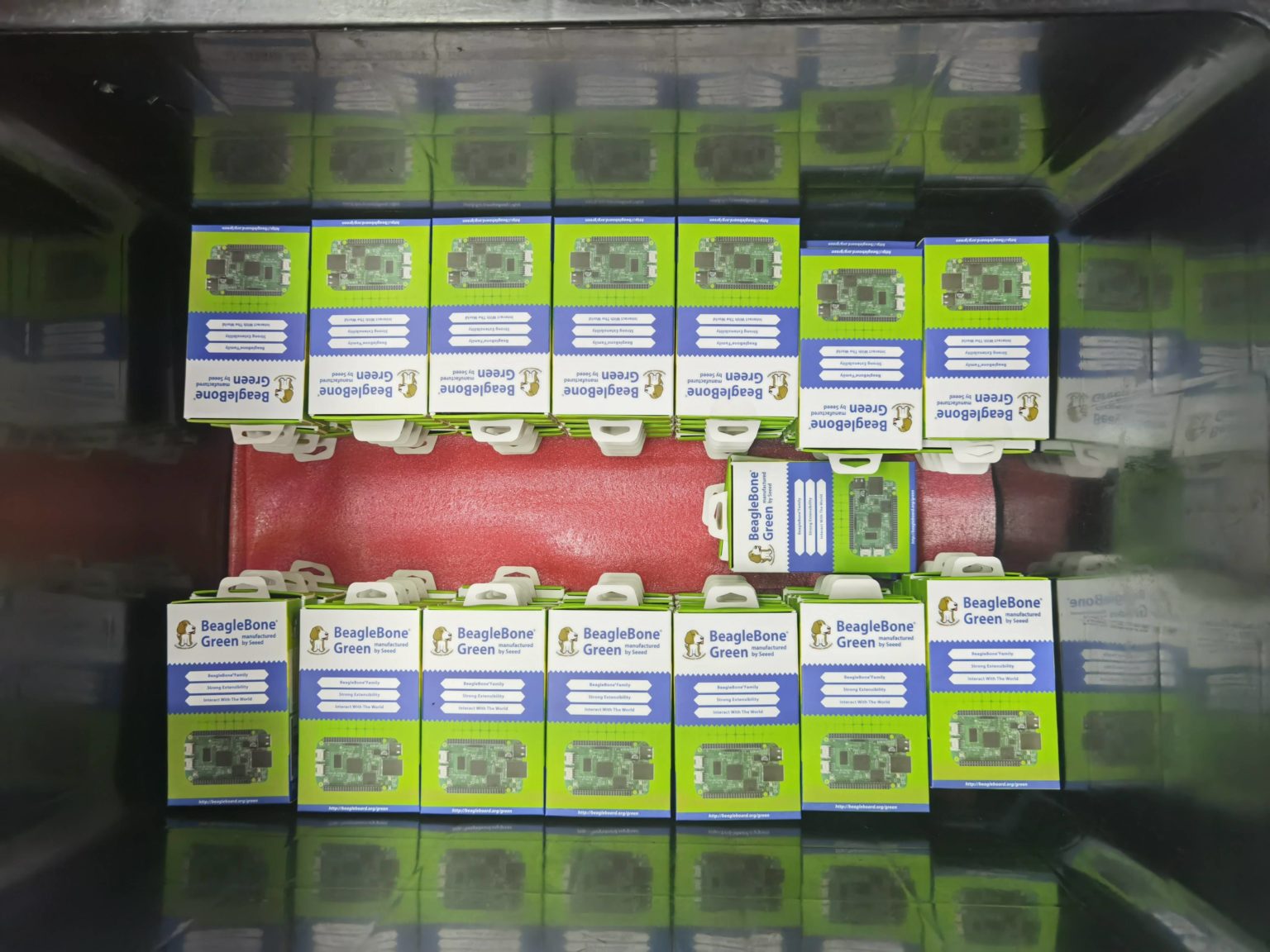
We are very pleased to see our BeagleBone Green manufactured in Vietnam, and are satisfied with the overall quality of it. With the help of experienced workforce and advanced equipment, our product can meet the necessary standards for reliability and functionality. We are delighted to begin our “Made with Vietnam” journey through this collaboration, and expect to see exciting developments in the future of a decentralized, open manufacturing.
Open Manufacture: Made with Vietnam S01E01
By Lily (May 19th, 2023)
We’re excited to share that, we’re going to have Seeed products manufactured at Telstar Factory in Bac Giang, Vietnam very soon.

Those of you who’ve been with us will agree that we owe our growth to the city where we’re based: Shenzhen, China, which has long been known as the “Silicon Valley of Hardware” due to its vast network of electronic manufacturing facilities. Back in 2008 when Seeed Studio was established, we manufactured all our products at our factory and our manufacturing partners’ facilities here in Shenzhen. Building our products close to home gives us the privilege to iterate quickly, applying lessons learned in production to make them simpler, and cheaper, to produce. Thanks to the vast resources of supply chain and international logistics, we can ship out the products and respond quickly to changes in demand from our global community.
However, we believe that this is the right thing to do: embracing decentralized manufacturing. The world of manufacturing is changing rapidly, with a growing emphasis on decentralized manufacturing, which enables the development of new products that can be customized to meet the specific needs of users. Rather than relying on a single manufacturing process and provider, decentralized manufacturing allows multiple parties to collaborate and work together, sharing information and knowledge along the way. Furthermore, decentralized manufacturing also democratizes the production of goods, promotes innovation and collaboration, and benefits the environment by reducing waste and minimizing the impact of transportation. By embracing this approach, we can create a more sustainable and equitable model for the production of goods, which will benefit us all.
Starting next month, we’ll be manufacturing Seeed Studio BeagleBone® Green at Telstar in Bac Giang, Vietnam, followed by other Seeed products in near future. In recent years, Vietnam, as one of the Association of Southeast Asian Nations, has become an increasingly popular destination for electronics manufacturing due to its strategic location, lower labor costs, and favorable policies for manufacturing and international trading. Some notable companies with manufacturing operations in Vietnam include Samsung, LG, Intel, Foxconn, Panasonic, Microsoft, etc. By sourcing and stockpiling components locally in Vietnam together with benefit from government incentives, we will be able to react more quickly to the rapidly increasing demand for our products in the global market.
Earlier this month, our team, comprising of experts in electronic manufacturing, logistics, and auditing: Founder and CEO Eric Pan, our COO Jessica You, and Project Manager Mandy Xiang visited various factories around Hanoi for the field study to screen out and decide our first global manufacturing factory in Vietnam (Vietnam is our 1st stop for global decentralized manufacturing operations and please do expect more to come). The followings are the wrap for their field study, and we’ll share more updates on “Made with Vietnam”. Stay tuned.
Team Landing in Hanoi
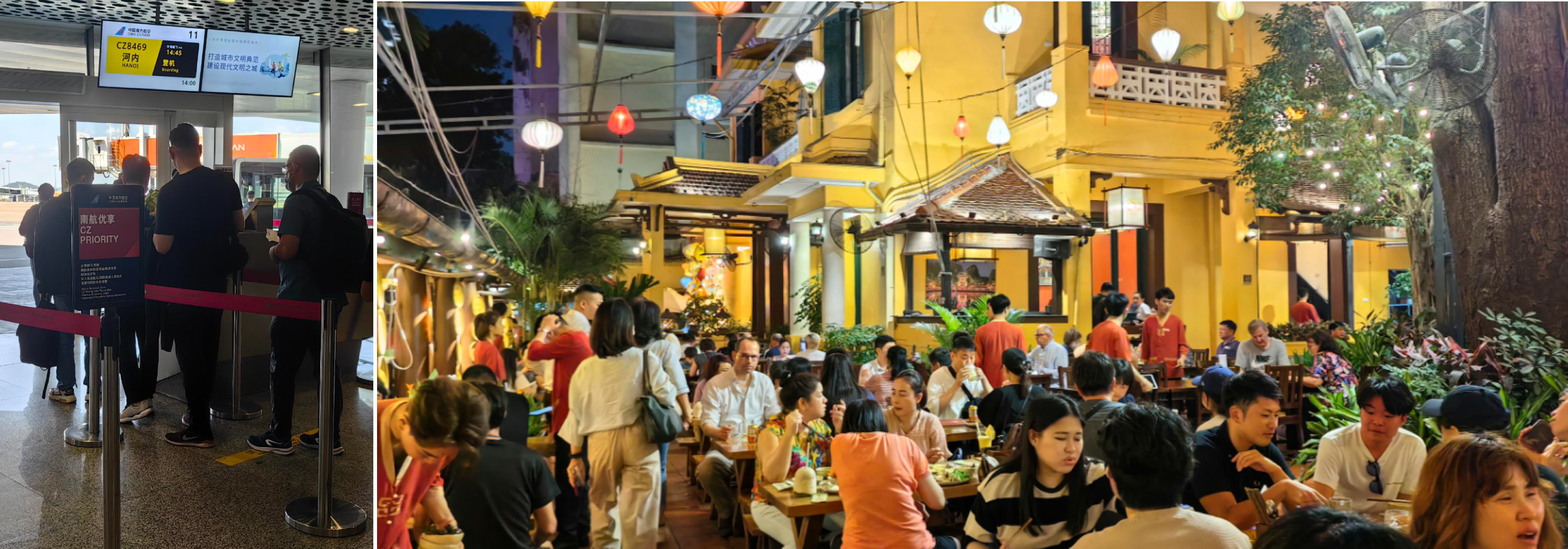
The goal for the field study was to gain a better understanding of the challenges and opportunities facing the industry and to identify best practices and areas for improvement.
Visiting Different Size Factories
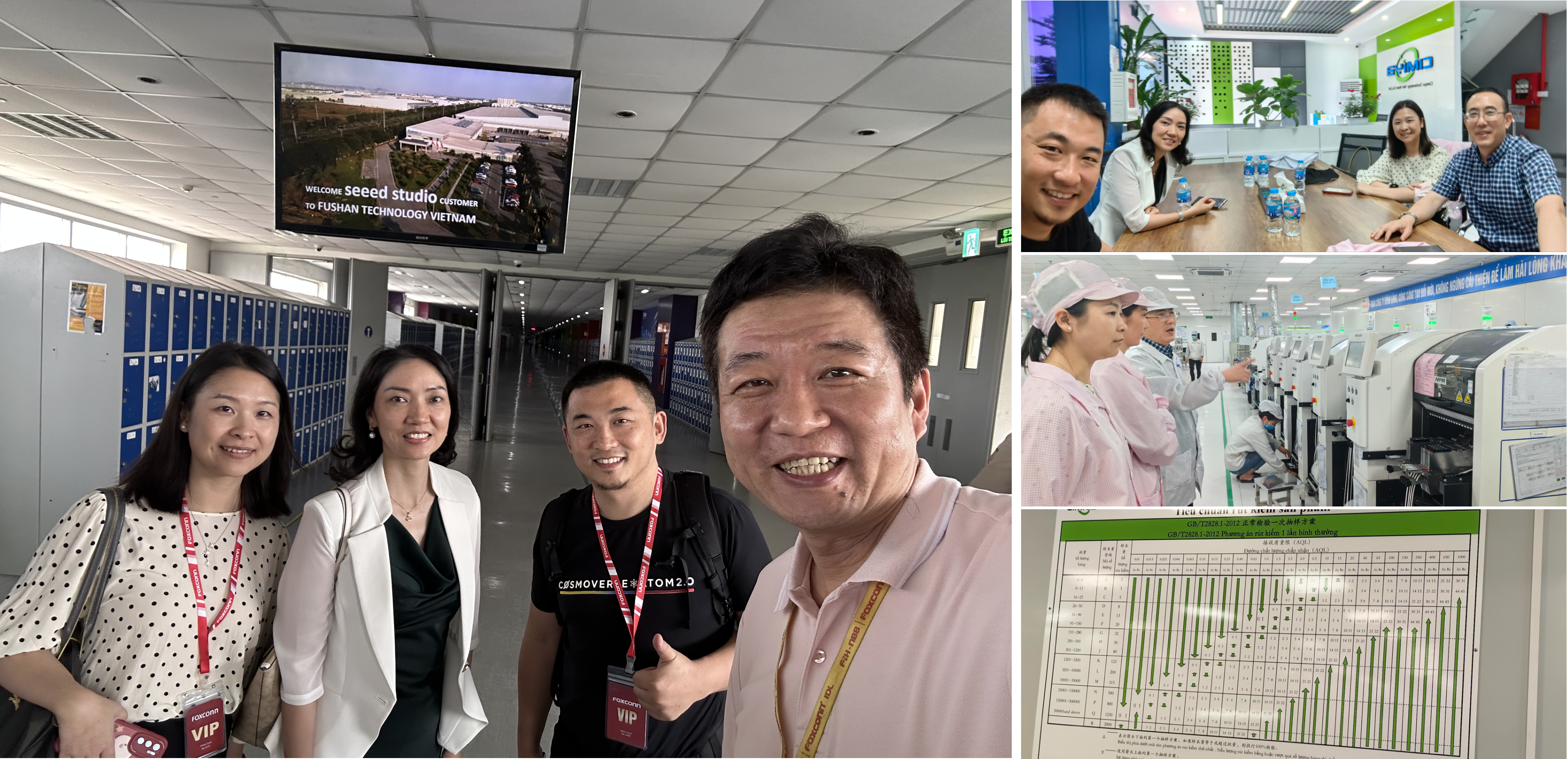
During the field study, the team visited several electronic manufacturing factories of varying sizes around Hanoi (mainly in Bac Ninh and Bac Giang provinces, where are well-known for electronic manufacturing). This allowed the team to gain a comprehensive understanding of the manufacturing processes, labor practices, and environmental impact of the factories. From the field trips, we learned that many factories had implemented innovative technologies and practices to improve manufacturing capacity and efficiency.
Partnership with Telstar
After careful evaluation and analysis of the different factories we visited, we decided to collaborate with Telstar to set up our operation base in Vietnam. Telstar has a strong capacity in OEM, as well as a dedication to ensuring the quality of products. Established in 2019, Telstar Vietnam is a high-tech enterprise of electronic products. Specialized in manufacturing projectors, dashcams, cameras, and PCBAs, Telstar offers OEM services for global clients. Telstar owns a modernized factory covering 14,000 square meters, 13 SMT lines, 500 workers, and 150 engineers in Vietnam.
We signed a strategy agreement with the factory to work together towards manufacturing Seeed products in Vietnam. As part of this partnership, we also put up our logo at the Telstar factory, demonstrating our commitment to manufacturing our products and joining the electronic manufacturing ecosystem in the country. And now, let’s look forward to the first batch of Seeed products manufactured in Vietnam.