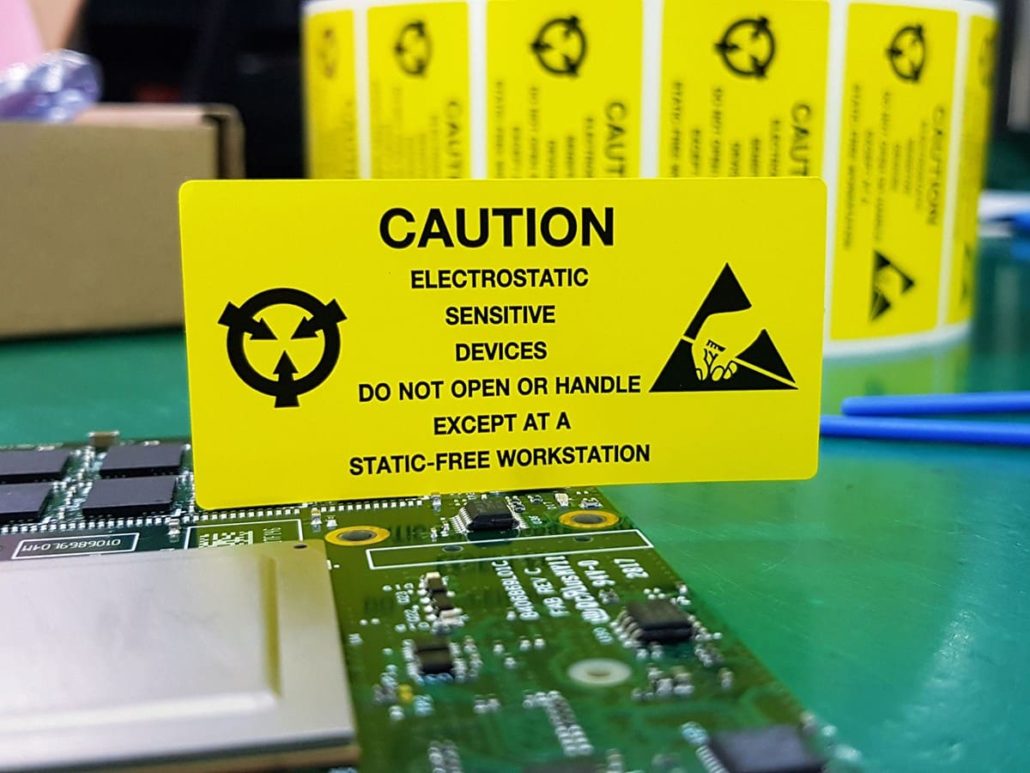
Why the ESD Protection is important?
Electrostatic discharge (ESD) can inadvertently damage expensive electronic equipment, resulting in a catastrophic failure out-front or premature failure in the field. In an electronics manufacturing setting, especially in today’s semiconductor age, even minor static charges can be detrimental to yield and longevity with estimates placing ESD damage at the fault of up to a third of product losses.
Electrostatic discharge, is the sudden release of built-up charge between objects, causing electricity to flow between them. Electrostatic discharge of charged objects generated by humans statically charged objects is enough to damage many semiconductor parts including MOSFETs, diodes and CMOS IC chips such as CPU and graphics ICs.
The build-up of static electricity in a person’s everyday movements is enough to cause permanent damage to electro-sensitive parts. While a part may not immediately fail, the invisible damage to parts can build up and cause the part to degrade, shortening the product’s lifespan and reducing durability. Typically, 60 to 90% of ESD damage does not result in complete failure but can be difficult or near impossible to detect. It, therefore, makes sense to reduce and control ESD during PCB assembly as much as possible.
ESD Control Strategies
A good ESD control strategy uses a combination of measures to reduce electrostatic charge in the work environment. Some methods are simple and inexpensive, while others may require major refurbishment or retraining of staff.
- Wear anti-static wrist straps or heel straps. ESD anti-static straps are a cheap and effective way of dissipating static from personnel. Wrist straps can be connected to a grounded line, keeping the person continuously grounded while they operate on sensitive equipment.
- Use conductive floor mats throughout the ESD-sensitive areas. Conductive floor mats help to discharge any static build-up on employee’s footwear and equipment.
- Require workers to wear anti-static clothing and shoe coverings. This not only protects from static but also contamination.
- Maintain a temperature and humidity between 22-18°C and 40-70% on the production floor. High humidity helps to prevent static from building up since moisture in the air can act as a conductor. Excessive humidity, however, can interfere with some equipment and moisture-sensitive parts.
- Connect racks and equipment to ground, and require personnel to discharge themselves before entering areas where ESD sensitive devices are being handled.
- Isolate and remove sources of static in the work environment. Limit the amount of insulating material in static sensitive areas such as paper, wood and plastics. Substitute standard equipment for non-static counterparts.
- Package parts and assemblies in anti-static materials such as pink anti-static bubble wrap, foam and ESD bags to protect them after they leave the production facility.
- Conduct periodic inspections to monitor ESD levels, locate sources of static and ensure employees are adhering to guidelines. Hold regular training sessions for both new and existing employees to reinforce guidelines.
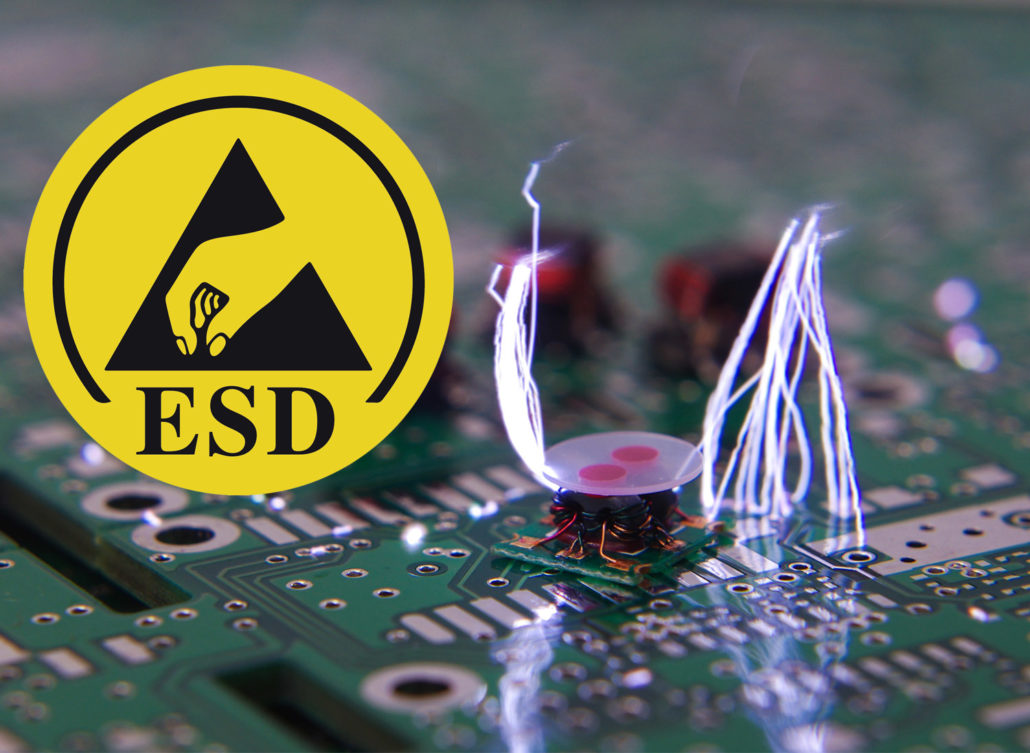
ESD is an invisible but serious threat in many electronics manufacturing facilities but with effective ESD management, electronics manufacturers can keep on top of static caused defects and realize greater yield, lower re-work workload, and improve the longevity and reliability of their products.
Seeed is an experienced, ISO9001 certified electronics manufacturer, specializing in PCB fabrication, components procurement and assembly. Seeed’s 12 years of agile manufacturing expertise ensures product reliability and flexibility to tackle a wide range of quality control issues. Click and learn more about our PCBA Capabilities.