Handling Moisture-Sensitive Devices for Automated PCB Assembly
Many of Seeed’s own products and consignments make use of surface-mount LEDs. Whether it’s WS2812, WS2813, SK6812, these digital individually addressable LEDs have delicate, sealed but permeable enclosures that encapsulate the individual LEDs and die chip.
In one particular PCB assembly case, more than 50% of the SMD LEDs in the batch had failed. Upon closer inspection, it was revealed that the LED exhibited die pad damage within the package.

This symptom, while difficult to detect with the naked eye, is characteristic of the popcorn effect or popcorn cracking, a result of rapid vapor expansion during soldering.
The popcorn effect occurs when excessive moisture in the permeable device is vaporized rapidly, such as during reflow or wave soldering. The sudden increase in gas volume causes cracking or delamination to occur between critical interfaces, resulting in the part failing immediately or sometime much sooner than its standard lifetime. In the case of SMD LEDs, the defect often manifests as peeling of the die from the base substrate.
Plastic BGAs and other components with organic compounds are also susceptible to moisture-induced damage. Often poorly prepared BGAs will give off a sharp crack sound during soldering, hence the name popcorn cracking. However, other less catastrophic defects can occur due to moisture sensitivity such as warping.
With the increasing adoption of lead-free soldering methods, and package form factors becoming smaller and thinner, the importance of proper handling and preparation of moisture sensitive devices is becoming all the more important.
Moisture-Sensitive Devices
SMT LEDs are classed as moisture sensitive devices (MSD) according to IPC/JEDEC J-STD-020B moisture sensitivity standards. More specifically, they are classed as having a Moisture Sensitivity Level (MSL) of 5a, which is the second-highest level. To maximize the production yield and lifetime of the devices, extra precautions, need to be taken during storage, handling and assembly.
The following are important points to pay attention to with a moisture control program as specified by IPC/JEDEC standards and from Seeed’s own assembly experience:
Incoming Parts Inspection
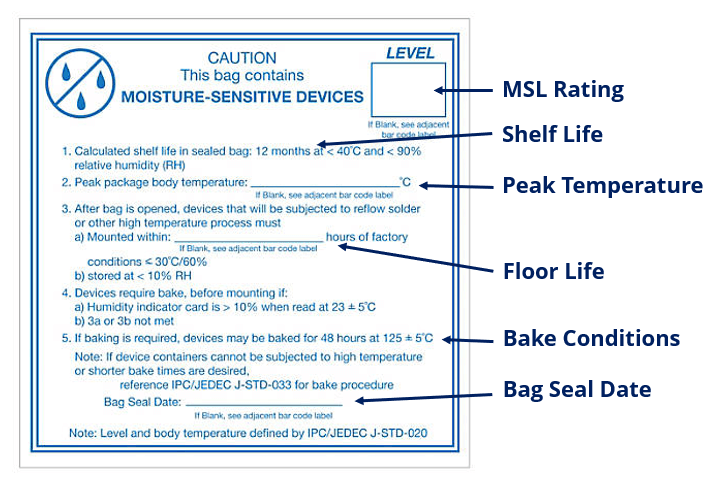
- When purchasing any moisture-sensitive device, it is important to ensure that the components arrive dehumidified from the supplier in airtight, moisture-resistant packaging, or moisture barrier bag (MBB). Check for any external damage to the packaging which may have caused the seal to be broken. If any exist, reject the package.
- The relevant moisture sensitive level (MSL) rating should be indicated on the packaging, along with stated shelf-life and floor life.
- Inside the MBB, a packet of desiccant should be included, along with a humidity indicator card (HIC). The HIC should be inspected immediately upon opening the packet to gauge the environment inside the MBB.
- Incoming parts inspection should be limited to half an hour and exposure should be reduced as much as possible. Vacuum seal and keep in a dry cabinet if possible.
Handling and Preparation
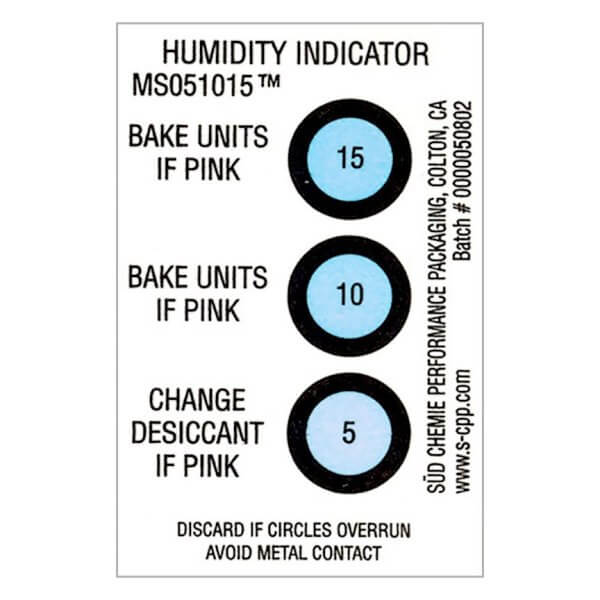
- It is good practice to inspect the HIC immediately upon opening the packet and replacing it with a fresh card with every use.
- The HIC should be used to gauge whether the parts are in need of baking. For high MSL devices (MSL 2a-5a), relative humidity in excess of 10% requires the devices to be baked before use.
- If the cumulative floor life has been exceeded, but the card does not indicate the need for baking, the parts should still be baked before use. The HIC is only indicative of the relative humidity in the MBB since it was replaced, and not the total exposure.
- Keep a detailed record of exposure times each time the devices are used and bake if the floor life has been exceeded. Baking resets the clock.
- Maintain ambient factory conditions (<30°C/60% RH) to reduce moisture permeation during handling and soldering and accurate floor life measurements.
Baking and Storage
- If not otherwise specified on the label, one may refer to the following table for baking times for different MSL devices, package thicknesses and baking conditions.
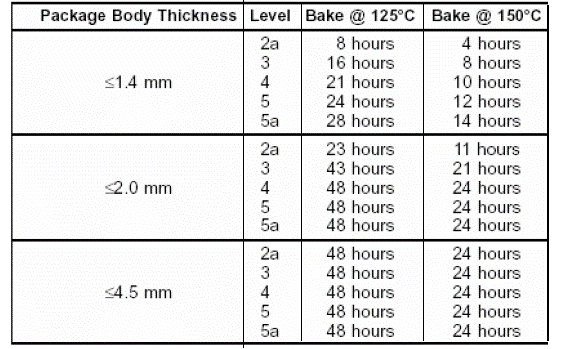
- Level 6 MSL devices must be baked before every use within the specified floor life.
- Care should be taken to avoid baking for too long or at higher than necessary temperatures to prevent oxidation and the formation of intermetallic compounds in the device.
- The relevant baking tray for the baking temperature should be used to prevent the formation of gases.
- The entire board should be baked if the device requires re-working to prevent damage.
The Seeed Fusion service has been providing convenient and affordable PCB manufacture, PCB assembly and other hardware manufacturing services for over 10 years. The online quotation platforms make instant and transparent quotations possible with a few clicks.
Fusion’s star service is the turnkey PCB assembly service which takes care of PCB manufacture, components procurement and assembly, so you can get on with design and testing. All PCBA orders come with free shipping worldwide and a wide variety of options and additional services are available such as expedited PCBA, Design for Assembly (DFA) review, testing and certification.