DC Motor vs Stepper Motor vs Servo Motor – Which Motor Should you Choose for Your Project?
From security cameras and fans to DVD players and right down to the vibration in your phone, motors are practically all around us. With so many variables to consider, it is hardly surprising that many find it difficult to choose the right motor for their application and miss out certain important parameters in the process. As such, we have put together a guide to help you choose between DC Motor, Stepper Motor and Servo Motor.

Without further ado, let us jump right into Choosing the Right Motor for Your Project – DC vs Stepper vs Servo motors!
Types of Motors
We will be looking at 3 common motors – the DC, Stepper and Servo motors, their applications, as well as their advantages and disadvantages.
1. Brushed and Brushless DC Motors
DC motors are electromagnetic devices that use the interaction of magnetic fields and conductors to convert electrical energy to mechanical energy for rotation. There are many types of DC motors out in the market. The brushed and brushless motors are the most common DC motors.

(Source: Alliedmotion)

Brushed DC Motors
The brushed DC motor has been around for a long time, and its use can be traced back to the 1830s. They are every way. In toys, household appliances, computer cooling fans, you name it. As one of the simplest motors to construct and control, it is no wonder that the brushed DC motor still remains a favourite among professionals and hobbyists alike.
Why are they called brushed motors? The current is provided via two stationary metallic brushes that make contact with the different segments on the ring. As the commutator rotates, the brushes make contact with the next segment and therefore continue the rotation of the motor. As you can imagine, this generates friction and so heat and even generated sparks.
Working Principle:
How does a DC motor move? DC motors include two key components: a stator and an armature. The stator is the stationary part of a motor, while the armature rotates. In a DC motor, the stator provides a rotating magnetic field that drives the armature to rotate. A pair of magnets, or a stator envelopes the coils in an electric field by surrounding the coils. When current passes through a wire in a magnetic field, the wire experiences a force, and so the coils in the motor experience a force that pushes the coil and begins the rotation. The GIF below illustrates the working principle of the brushed motor.

(Source: Renesas)
The coil experiences a downward force when it reaches the area on the right, and an upward force when it reaches the area on the left. By adding multiple coils attached to different segments on the commutator, it can maintain steady rotation. You can reverse the direction of rotation simply by reversing the polarity on the motor’s contacts.
Advantages & Limitations of Brushed DC Motor
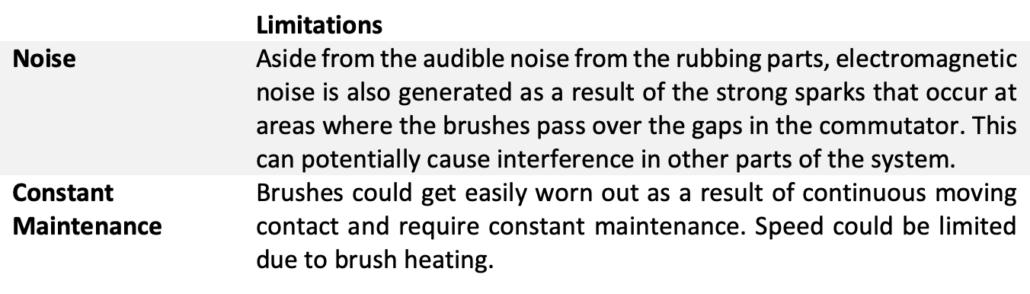
Find inexpensive DC motors at Seeed Bazaar!
Applications of Brushed DC Motors:
Nowadays, some might claim that the brushed DC motors are no longer relevant as the brushless motor has displaced it from many applications. However, that is definitely not the case.
Brushed motors can still be the best solution for many industrial applications that require constant torque across the motor’s entire speed range. Uses include mobile phone vibrators, toys, handheld fans, cordless drills and car windows among many things.
Depending on the needs of your application, the brushed DC motor might be the more suitable option. If a simple control scheme and low cost is your primary concern, consider the use of a brushed DC motor.
Brushless DC Motors
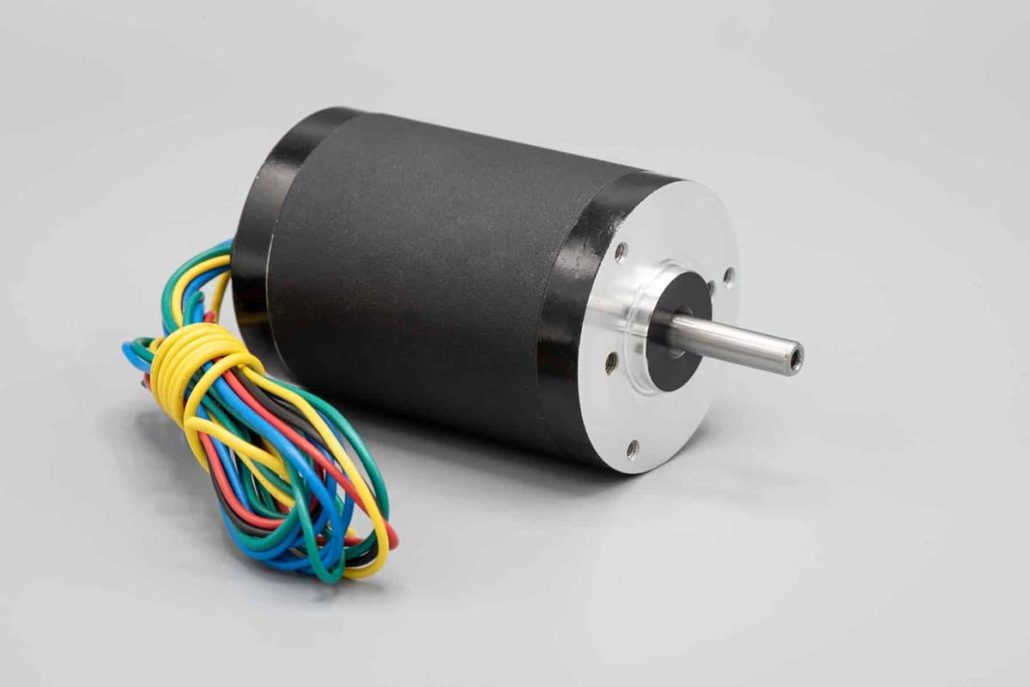
Brushless DC motors are mechanically simpler than brushed ones. As commutation is achieved electrically, the sparks and noise of brushed DC motors is eliminated, enabling the current flow to switch silently and therefore allowing the motor to be driven quietly. These quiet motors find applications in computer fans, disk drives, drones, electric vehicles and high-precision servomechanisms.
Working Principle Brushless DC motors:
The brushless DC motor only has one moving component – the rotor, which eliminates the complications caused by brushes in brushed motors. And also unlike brushed motors, the rotor consists of a ring of permanent magnets, whereas the coils are stationary. This set-up eliminates the need for brushes.
The difficult part comes in controlling the polarity of the current flowing through the coils and keeping this in sync with the speed of the rotor. This can be achieved by measuring back EMF or using Hall effect sensors to directly measure the position of the magnets.
Due to this, brushless DC motors are typically more expensive and complex, in spite of the numerous advantages it has over brushed DC motors.
Advantages & Limitations of Brushless DC Motors:
Applications:
Thanks to their efficiency and durability, the brushless DC motors have largely supplanted their brushed counterparts. They find a wide range of applications in devices that run continuously, such as washing machines, air conditioners, and in consumer electronics like computer fans and disk drives. More recently, they are used for drones as the rotational speed of each rotor can be precisely controlled. In the near future, we can definitely expect more applications for brushless motors!
2. Stepper Motors
Stepper motors are motors that move in slow, precise and discrete steps. Valued for their precise position control, they find a myriad of applications such as desktop printers, security cameras, and CNC milling machines.
Working Principle:

An operating Stepper motor
(Source: emmeshop)
Stepper motors have a controller system that sends electrical pulses to a driver, which interprets these pulses and sends a proportional voltage to the motor. The motor then moves in accurate and fixed angle increments, hence the name “stepper”. The stepper motor works similarly to brushless DC motors, except that it moves in much smaller steps. Its only moving part is also the rotor, which contains the magnets. An alternating current controls the polarity of each coil. As the polarity changes, each coil gains push or a pull effect, thus moving the motor.
We can use commonly available and cheap microcontrollers to control stepper motors. However, a stepper motor is a power-hungry device that constantly draws maximum current. The small steps it takes also means that it has a low top speed, and steps can potentially be skipped when high loads are used.
Advantages & Limitations of Stepper Motors:
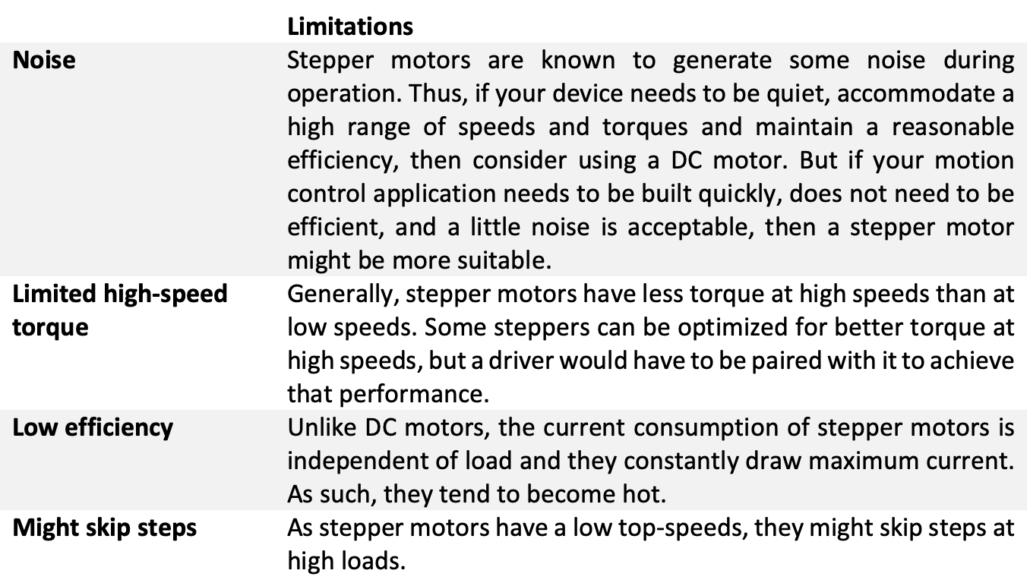
Applications of Stepper Motors:
Stepper motors are diverse in their uses and are found in a myriad of common machines and equipment. They are useful in applications that require accurate positioning, low speed torque, and speed control. Applications include CNC milling machines, medical imaging machinery, printers, car side mirror tilts, security cameras, robotics, and more recently, 3D printers.
3. Servo Motors
Servo motors are motors capable of providing very precise motion control. The feedback in a servo motor system senses the difference between the actual and desired speed or position so that the controller can adjust the output to correct any drift from the target position. The positional rotation and continuous rotation are two basic types of servo motors
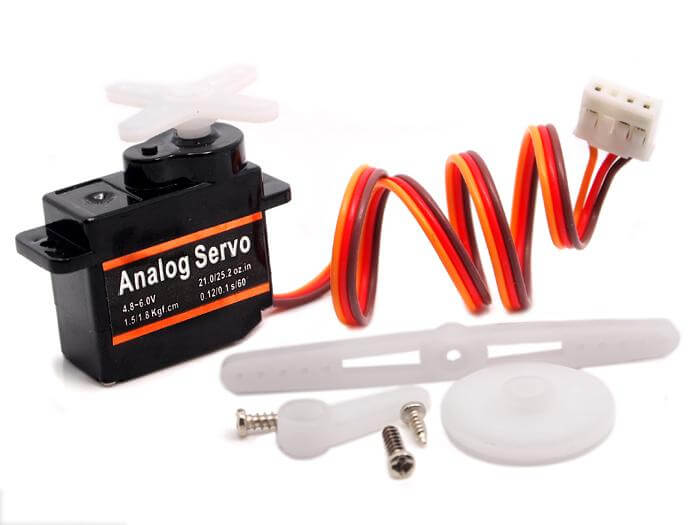
Working Principle:
The servo motor consists of a DC motor but not Servo motor. DC motors spin at high rpm and very low torque. However, inside a servo motor, there is an arrangement of gears that will take the high speed of the internal DC motor and slow it down, while at the same time increasing the torque. Thus, the gear design rotation speed of the servo is much slower but with more torque. Gears in a cheap servo are typically made of plastic to keep it light and to keep the costs down. But for servo motors designed to provide more torque for heavier work, they usually use metal gears.
A servo contains a positional sensor, or encoder, on the final gear. Based on closed-loop control, the microcontroller compares the actual position of the rotor to the desired position and generates an error signal. This error signal is then used to generate the appropriate control signal to move the rotor to the final position. More sophisticated servos also measure speed to provide more precise and smoother movement.
Positional rotation servos – Widely used for small-scale projects where moderate precise positioning is required, this is the most common and inexpensive type of servo motor. This servo motor rotates within a 180 degrees range. They do not provide speed control or continuous rotation. It has physical stops built into the gear mechanism to prevent turning beyond these limits to protect the rotational sensor.
Continuous rotation servos – Unlike the positional rotation servos, the continuous rotation servo can turn clockwise or anti-clockwise continuously, at varying speeds depending on the command signal.
Here’s an animation from learnchannel about the functioning of a servo motor and how the components of a servo drive system work together.
Advantages & Limitations of Servo Motors:
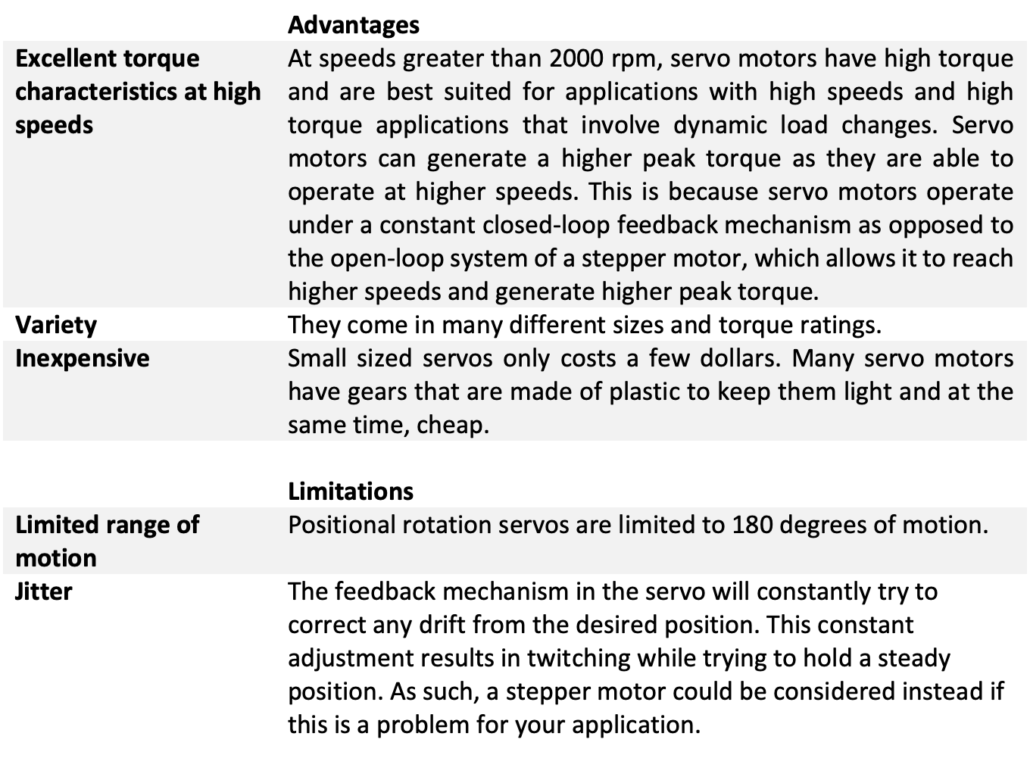
Summary
With that, the features of DC, Stepper and Servo motors provide information for you while selecting different motors. Specifications such as velocity, torque, current and voltage will also determine which motor is optimal for your project, so be sure to pay attention to the requirements needed.
As every project is unique, one factor will often hold more weight than the other in the decision-making process. By understanding what motors are available and developing a clear set of project parameters, you can avoid costly mistakes and select the best motor for the job.
Suggested Readings
Are you new at motors and unsure of how you can start tinkering with them? That is why Seeed created the Grove system, an easy-to-use, plug-and-play system specially developed for beginners. It takes a Lego-like approach to assemble electronics, simplifying the traditional, messy method of using breadboards and jumper wires. We even provide guidance PDF documents to introduce Grove and get you started. Try out the Grove here.
Also, check out our dummies guide on how to operate a 28BYJ-48 stepper motor with a ULN2003 stepper motor driver board and an Arduino. The Seeed Bazaar also stocks up a range of DC, Stepper and Servo Motors for you to choose from.
Do you have any additional advice regarding what to consider when selecting motors? Do let us know in the comments section below.
I have a project that has similarities to operation of 2 identical but reverse rotation motors/propellers that are commonly used for drones. My project does not involve any flying. I would appreciate your help in selecting the right kind of motor, controller and battery for the following. My design is to convert generated rotational momentum into some versatile linear propulsion using two sets of rotational masses within closed paths that are exact mirror images and their movements are synchronized mirror images. My goal is to generate a high level of rotational momentum, and convert that into linear propulsion, neutralize majority and end up with some measurable net linear propulsion, no matter how small the net propulsion is. On the one hand, the idea is physics based and should be able to formulate all movements into some computer simulated model, which seems as an easy, reliable and fast method. On the other hand, establishing such formulas for so many movements as basis for computer simulation is not an easy task. I find it more feasible to prove it by making a functional prototype instead. I am happy to realize similarities of movements between my project with those employed for flying drones. I am hoping that I might get some expert’s opinion from those using this site.
I selected a pair of CW and CCW 3-blade 6/4 Master Airscrew propellers for a practical prototype size, used 2 sliding pvc tubes on each blade to allow telescopic movement for extending their length to 20 cm when desired. Each of the blades will be connected to a small roller wheels. The wheels role against a vertical closed rail guard when rotating. Propellers are not used for flying but used to enable rollers mass as means of generating rotational momentum. The main work of any motor would be to rotate the modified and heavier blades which weigh 5 g/cm within the 20 cm length for a total of 300 g for 3 blades plus 3 of 75 g each of the wheels at the outer end of each blade for 225 g for 3 blades, for a total of 525 g per propeller and 1050 g for the 2 propellers. Propellers also slide against a flat horizontal plane to prevent propellers from bending. Required rpm values range from 50 to 300 (or 60, 90, 120, 180, 240 and 300) which do not need to be achieved quickly. What is of the highest priority is that the 2 motors are identical but turn the 2 propellers accurately in opposite directions as synchronized mirror images, at various speeds. I am allowing 50% friction factor for movements of propellers and rolling of the wheels. There is no lifting of any parts, and/or quick acceleration or other loads to be considered.
Are you making a contra-rotating propeller? I know that is not what you are asking for, but I am interested as to what you are making.
10 January 2020
Thanks for your note. I am not making any kind of propeller. I am modifying a propeller by enabling it to rotate some mass in a closed non-circular path, to generate some momentum, which hopefully be generating some net positive linear propulsion.